Induction motors are the most common motors in use today. Motor noise can be a challenge for most motor manufacturers. So what causes motor noise and what can be done to reduce the noise? In this article we will discuss where motor noise comes from and how it can be minimized.
The three basic types of motor noise are:
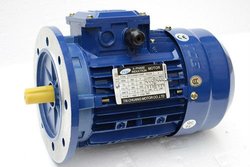
1. Magnetic Noise
2. Bearing Noise
3. Unbalance Noise
MAGNETIC NOISE:
The main source for magnetic noise in induction motors comes from force waves created by the rotating magnetic field. Since this field is the vehicle by which power is transmitted from the stator to the rotor, elimination of this noise is not possible. However, magnetic noise can be minimized by utilizing several techniques:
1. Using the correct stator and rotor slot combination
2. Designing the stator and rotor lamination geometry
3. Applying the proper coil pitch
4. Formulating the appropriate rotor skew
The proper selection of stator and rotor slots is one of the most important aspects of a quiet motor design. This selection also affects manufacturing costs. To keep manufacturing costs low, the number of stator slots should be the number of poles times the number of phases within a given frame size. This number of stator slots should be such that a balanced winding can be accommodated. There are hardly any slot combinations that are perfect; however, over the years there have been some combinations that have proven to be successful. The following general rules should be used as a guide when designing the lamaintions:
a. The number of rotor slots should not equal the number of stator slots. Acceptable performance has been attained when the number of rotor slots differs by the number of stator slots by 15 to 30%. b. To avoid dead points or cogging, the difference between stator and rotor slots should not equal +/- number of phases times number of poles c. To minimize noise and vibration the difference between the number of stator slots and rotor slots should not equal +/-1, +/-2, +/- (number of poles+/-1) and/or +/- (number of poles +/-2). For example: if you have a 6 pole motor and the stator lamination has 18 slots then the rotor laminations should not have the following number of slots: 17, 19, 16, 20, 13, 23, 14, or 26.
When designing the stator and rotor lamination geometry, many parameters must be reviewed. A closed rotor slot will cause less permenace variation, however, thickness of the bridge must be reviewed to ensure the lamination does not saturate. The width of the stator slot opening should be kept to a minimum however; you still need it large enough to insert the coils. The length of the air gap also affects permeance variation such that the larger the gap the less the variation. But keep in mind, the air gap also is dependent on the other design criteria such as power factor and efficiency. The motor design engineer needs to take into account all requirements when designing laminations.
Utilizing the proper stator coil pitch is additionally important. The stator coil pitch ratio should be selected to give small pitch factors for lower order of air gap harmonics. The motor designer will need to keep this in mind when designing the winding. Skewing of either rotor or stator slots is another way to reduce motor noise and provide smooth acceleration. The degree of skew also affects motor performance, therefore the skew is limited to performance parameters such as breakdown torque, starting torque and starting currents.
BEARING NOISE
Bearing noise can be influenced by several factors such as preload, shaft to bearing fits/tolerances, and bearing to bore fits/tolerances. The decision to which bearing to use should always depend on the application of the motor. It is highly recommended to involve bearing manufactures when choosing the bearing.
Proper preloading is required to ensure the bearings run smooth. Too much preloading will damage the bearings. Same philosophy goes with the bearing fits to the motor shaft and housing and end bell bores. Bearing manufactures have recommended fits/tolerances to implement during the mechanical design of the motor.
UNBALANCE NOISE
Unbalance noise is created by an unequal weight distribution of the rotor assembly around the motor axis of rotation. It has been found that vacuum impregnation and/or encapsulation of motor stator windings has also helped in coil vibration and noise. There are many ways to reduce motor noise. All motor parameters must be taken into account when designing the unit.
Categories
- 18671914 (1)
- 18701920 (1)
- ACcommutator (1)
- ACDC (1)
- Actuators (1)
- AlternatingCurrent (1)
- America (1)
- Analysis (1)
- Application (2)
- Applications (7)
- Automation (1)
- Bearings (1)
- Before (1)
- Benefits (1)
- Best (2)
- Better (1)
- Between (2)
- Biography (1)
- Book (1)
- Brands (1)
- Building (1)
- Business (1)
- Buy (2)
- Cambridge (1)
- Century (1)
- Changing (1)
- Cheap (6)
- Checking (1)
- Choosing (1)
- Circuits (1)
- Citadel (1)
- Combustion (1)
- Common (2)
- Comparison (1)
- Computer (2)
- Condition (1)
- Conditioning (1)
- Construction (2)
- Control (6)
- Controls (3)
- Conversion (4)
- Conversions (1)
- Convert (1)
- Creating (1)
- Deal (2)
- degree (1)
- Degrees (1)
- Design (6)
- Designers (1)
- Determining (1)
- Difference (2)
- Differences (1)
- Different (1)
- Discount (7)
- Doesnt (1)
- Drives (7)
- Dryers (1)
- Dynamic (1)
- Edison (1)
- Edition (5)
- Electric (24)
- Electrical (4)
- ElectricElectronic (1)
- Electricity (3)
- Electronic (1)
- Electronics (1)
- Energy (2)
- Engineering (5)
- engineers (1)
- Engines (1)
- Enron (1)
- Essential (1)
- Everything (1)
- Explained (1)
- FaultDiagnosis (1)
- Faulttolerant (1)
- Features (1)
- Freedom (1)
- Functions (1)
- Fundamentals (1)
- Future (1)
- Gearbox (1)
- Generation (1)
- Generator (1)
- Genesis (1)
- Genius (1)
- Get (2)
- Guide (2)
- Guides (1)
- Handbook (3)
- Harnessing (1)
- Histories (1)
- HP1568 (1)
- Hydraulics (1)
- Impact (1)
- Important (2)
- Induction (7)
- Industrial (4)
- Industry (1)
- Innovations (1)
- Inventions (1)
- Inverter (1)
- Knowing (1)
- Lasting (1)
- Lights (1)
- Locomotives (1)
- Machine (3)
- Machinery (3)
- Machines (1)
- Magnetic (2)
- Magnetism (1)
- Maintenance (3)
- Making (1)
- Materials (1)
- MATLABSIMULINK (1)
- Mechanical (1)
- Microwave (2)
- Mighty (1)
- ModelBased (1)
- Modeling (1)
- Modern (1)
- Monitoring (1)
- Monographs (1)
- Motor (1)
- Motorcycle (1)
- Motors (20)
- motorsincluding (1)
- Nature (1)
- Nikola (1)
- Operation (1)
- Performance (3)
- Plants (1)
- Pneumatics (1)
- Popular (1)
- Power (1)
- Practical (1)
- Principles (1)
- Problems (2)
- Reconnecting (1)
- Recovery (1)
- Reference (1)
- Related (2)
- Repair (2)
- Review (1)
- Reviews (3)
- Revolutions (1)
- Rewinding (1)
- Rotating (1)
- Savage (1)
- Science (2)
- Secret (1)
- Sensors (1)
- series (1)
- Should (1)
- Simulations (1)
- singlephase (1)
- sixphase (2)
- Specification (1)
- Speeds (1)
- Spiral (1)
- Stainless (1)
- Standards (1)
- Stepper (1)
- strategyChinese (2)
- Suppressed (1)
- Synchronous (2)
- System (1)
- Systems (4)
- Take (1)
- Technical (1)
- technicians (1)
- Techniques (2)
- Teslas (1)
- Theory (2)
- Things (1)
- Torque (1)
- Transportation (1)
- Treadmill (1)
- Troubleshooting (1)
- Twentieth (1)
- ULTIMATE (2)
- Utility (1)
- Variable (2)
- Vector (1)
- Vehicle (4)
- Vehicles (1)
- Vehicular (1)
- Vertical (1)
- Washing (2)
- Wheelwork (1)
- Willis (1)
- Wizard (1)
Archive
-
▼
2013
(77)
-
▼
February
(43)
- *Hot Deals Electric Motors and Drives: Fundamental...
- Electric Vehicle Motor For Conversion - DC Motor O...
- ~~Take Modern Electric/Electronic Motors*
- Electric Car Parts - Important Things You Should K...
- ~Cheap The performance and design of A.C.commutato...
- Features of Servo Motor Repair and Gearbox Repair
- ~~~Get Ac Motors for High Performance Applications...
- Changing an AC Motor
- *Discount AC/DC: The Savage Tale of the First Stan...
- DC Power in Industry - Mighty Torque and Variable ...
- >>>Cheap Build Your Own Electric Motorcycle (Tab G...
- AC and DC Drives - How to Buy
- ~Deal Power Electronics in Motor Drives: Principle...
- ***Deal novel six-phase AC induction motor control...
- A Review Of Andis Hair Dryers - Are They Any Good?
- *Hot Deals The Electric Vehicle Conversion Handboo...
- ***Buy Suppressed Inventions**
- Types of Stepper Motor and Its Important Benefits
- Stair Lifts and Electric Stair Lifts
- **Discount Electric Motors and Control Techniques~~~
- ~~Best buy Ac Motors for High Performance Applicat...
- Building a Wind Generator
- >>>Cheap Vehicular Electric Power Systems: Land, S...
- EV Car Kits - Choosing a Motor For Your Vehicle
- ***Discount The ULTIMATE Tesla Coil Design and Con...
- Stainless Steel Pump for Oil Spill and Recovery Ap...
- *Hot Deals Spiral Vector Theory of AC Circuits and...
- >>>Buy Control of Electrical Drives***
- >>Deal Practical Electric Motor Handbook<<<
- >>>Discount Wizard: The Life and Times of Nikola T...
- ~~~Reviews Dynamic Simulations of Electric Machine...
- The Difference Between AC and DC Electric Motors
- *Hot Deals Electric Motor Maintenance and Troubles...
- AC Inverter Drive's Power Stage - Basic Operation ...
- Industrial Electric Motors - A Comparison of Its D...
- Electric Motor Types
- Electric Motor Applications
- Washing Machine Motors - Common Problems Related t...
- Induction Motor Noise
- What Is an Induction Electric Motor?
- Differences in AC Motor Controls
- Electric Motors for Cars
- Determining Which Motor is Right For You
-
▼
February
(43)
0 comments:
Post a Comment